投稿日:2021年7月5日
私たちOEM装置設計・製造.comでは、医療機器や食品機械などの装置を材料や購入品の手配から始まり機械加工・組立・電装・調整してご指定の納期までに完成品を納入させていただく…といった社内一貫の装置製造を行っております。
今回はお客様のご要望があり、このページの運営会社「ZESTIA(以下“当社”)」にてユニットや電気の設計・開発を行った事例のご紹介となります。
電装ボックス内部の基板化によって30%のコストダウンにつながった事例になります。
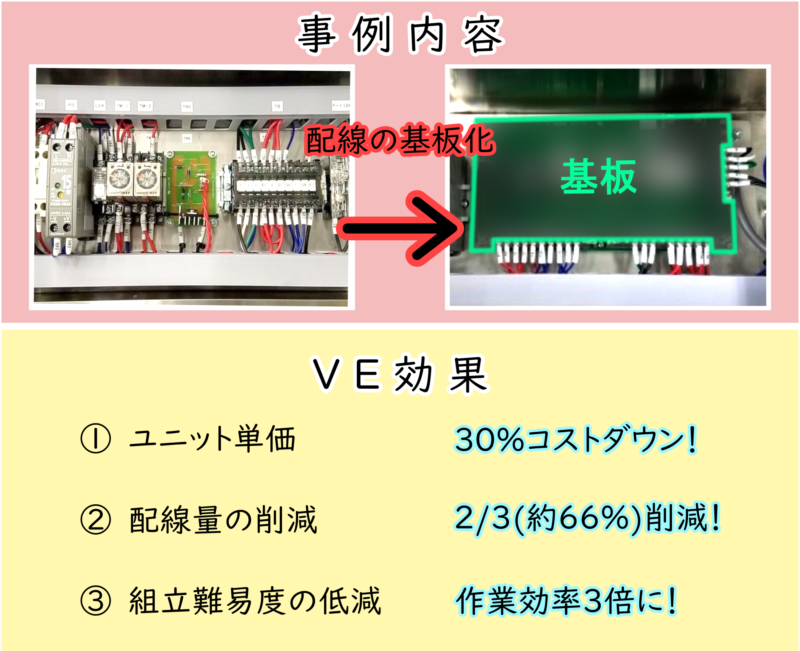
1.製作に至る経緯
当社は基本的にお客様の設計されたものを基に製造させて頂いているのですが、この事例はお客様からのご依頼で、計量器に取り付けるフィーダーを当社にて設計・開発するに至った案件になります。
お客様の「計量器」に付属するユニットとして「フィーダー」が必要になったのですが、お客様としても開発費を抑えたく、設計・開発を現行の取引企業様(電気関係)と合わせて当社に相見積りの形でお話を頂いた…というのが始まりです。
当社としてもお客様の装置の経費削減の一助になればと取り組み、まずはお客様のニーズの汲み取りを入念に行った上でお見積りを提出し、ご依頼をいただきましたので、試作へと進みました。
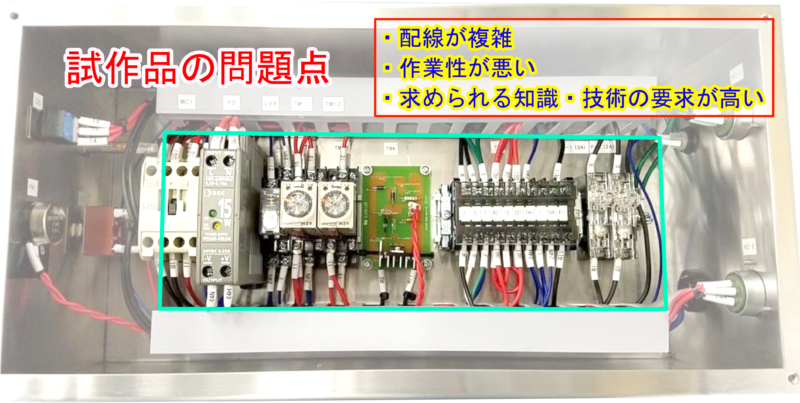
2・試作に当たって浮き彫りになった問題点
こちらが初めに当社が設計した電装BOXになります。お客様とのお打ち合わせももちろんですが、この電装BOXが設置される装置自体の製造・組立を社内で行っていたこともあり、お客様とのすり合わせも2回ほどで製作にこぎつけました。当社の設計部門の担当者が全て組み上げ、お客様にもご満足いただけたため、正式に採用頂く事になりました。
ですが実際に試作品の製作をする中で、今後の量産を考えた場合の問題点も出てきました。
〇問題点
・複雑さも相まって属人的な作業内容となってしまった
・組み上げにかかる時間(工数)の削減が必須
・コストの低減が必要
➢教育の時間も費用も削減できないか?
当社所属の組立人員も電気の知識は多少ございますが、専門家ではありません。お客様に納品する上で不良品はもってのほかですし、作業内容を1から教育となると余計に時間も掛かってしまいます。専門家でない組立人員が製品を問題なく組み立てることができるようにならないか?というのが課題となります。
➢特に時間のかかる配線作業の改善ができないか?
人員の幅が広がっても組立に時間がかかってしまうようであればコストダウンの効果は薄れてしまいます。設計者が行う組み上げに近しい時間・品質で他の人員も組み上げられるような変更が必要になります。それには誰が見ても一目瞭然で組み上げができるようなユーザビリティの向上が必須となります。
➢コストダウンの必要性
お客様から求められる機能は達成していましたが、試作段階でのコストパフォーマンスは十分に良い状態とは言えませんでした。お客様へのご提案にもつながることですが、社内で製品の製造単価を削減するため、加工・組立・電気など多角的に見直す必要がありました。
問題点を踏まえて、下記の改善後の内容をご覧ください。
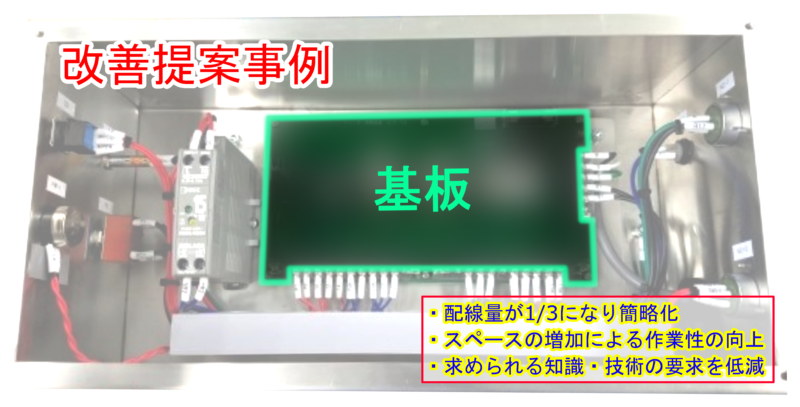
3・VE内容とその効果
- 配線の2/3を基板に実装→使用する配線が1/3に!
少々隠させていただいておりますが、緑で囲った部分が基板となっており、配線を基板上に回路として実装しました。これによってリレーなど電装部品をつなぐために大量に必要だった配線を2/3程削減することができました。もっと予算をかけることができればより多くの機能を基板のみで完結することもできますが、今回はもともと決まっている予算の中で改善をする必要があったので、主に配線のみを基板に実装することで【作業性の向上】につなげることができました。
配線に関しては「この部品にはこの配線」が必要だから…と、必要最低限に抑えてはいましたが通常通り使用していました。ですが代替となりうる削減案を十分に検討できていなかったのも事実です。日々のコストダウン提案でも頻出しますが、先入観を一旦脇に置いておくことも時には必要となります。当社としても見直す段階になってやっと先入観を除いて考えることができました。
- 電装部品の設置位置・配線位置の明確化
基板への端子接続部分には、各配線の番号が印字されています。これにより、配線時のヒューマンエラーの低減と、組み上げに必要な専門性の低減を実現することができました。また、配線が少なくなったため作業性も向上。電装部品の配置も含めマニュアルを作成したことで誰でも簡単に組み上げられるように改善されました。作業内容の単純化をしたことで熟練者との「作業時間・作業の正確性」の開きは低減し、作業担当者を増やすことによる「時間効率の低減・不良率の増加」を防ぐことができました。
- コストダウン
あくまでコストを抑えつつ基板化による作業効率の向上を目指した本件ですが、前述の通り配線のみを基板化したことでイニシャル費もかなり抑えることができました。元々の試作品と比べ、 (購入品や加工品の調達・製作する数が) 同条件でも30%のコスト削減となっております。
今回の製品は中量生産だからこそ、イニシャル費を抑えた基板化となります。機能をすべて盛り込むことでより高性能、且つ単体でほとんどの機能を賄うことも可能ではありますが、イニシャル費はかさんでしまいます。また、この製品に関してはパネル・操作盤の関係上中身の小型化ができても外箱はそのままのサイズになることもあり、これ以上の機能の実装は費用対効果を考えて「適切ではない」と判断した次第です。このあたりのバランスについては、その製品のリピート性や「抱えている問題点」の解決に必要な要素かどうか…等、案件ごとに判断が必要になります。
※機能詰め込み型の基板に関しても良い事例がございますので、またの機会にご紹介させていただきます。 ご興味のある方はお楽しみにお待ちくださいませ。
4・まとめ
今回の事例は、単発品とリピート品の違いとでも言いましょうか、「機能を満たしているから良い」というだけではなく、作業性のアップによる単価低減・納期の改善など、お客様はもちろん社内にもメリットの多い見直し事例となりました。
技術のある人員に頼りがちになってしまうことも普段少なくないと思います。それは何も設計に限った話ではなく、加工や組立等様々な部署でも起こりうることだと思われます。その際に教育にリソースを割くことをいつの間にか避けてしまっていませんでしょうか?当社でも悩むことの多い問題なのですが、今回のように作業内容の見直しによって割くべきリソース自体の低減も可能なのです。
今お手元にある図面も、今一度設計を見直してみてはいかがでしょうか?
設計の見直しを実行される際、様々な事例を集めたハンドブックもご用意しておりますので、必要な方はお気軽にお声がけください。このサイト「OEM受託設計・製造.com」も、これからも随時更新して参りますので、お役立ていただけましたら幸いでございます。
最後までお読みいただき、ありがとうございました!