投稿日:2021年1月13日
私たちZESTIAでは、医療機器や食品機械などの装置を、材料発注から機械加工・組立、そして納品するまで一貫して対応するOEM受託組立製造を行っております。
今回ご紹介するのは、はめ合いの2部品を工程集約で1部品にまとめ、旋盤・フライス両方での加工→フライスのみの加工で完結させる設計変更を実施。結果として幾何公差などもクリアした状態でコストを35%削減できた事例になります。
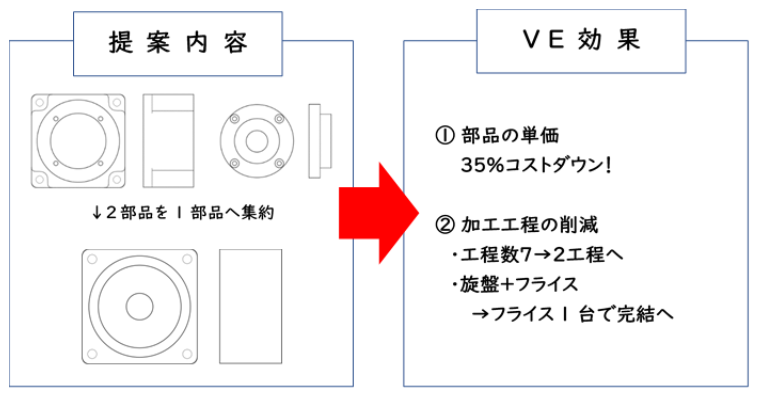
今回ご紹介するのは、多種多様な産業機械を取り扱っておられるメーカー様からコストダウンの相談を頂き、設計の方を含め提案させていただいた結果、上記の効果が実現できた事例になります。
・産業機械メーカーA社様の事例
この事例は、弊社が取引をさせて頂いているある産業機械メーカー様のお話です。かなり精度の要求が高い機械を扱うA社様では、機械1台の値段がどうしても高くなってしまう現状にお困りでした。ご想像の通り、部品の中には要求される加工精度の高いものが多数あり、製作にかかるコストが高くついてしまうためです。
そこで弊社は図面をお預かりし、VE(コストダウン)提案のご依頼を頂きました。いつも通りすべての図面を見直しましたが、加工難度が上がればその分製作時間もかかるため、図面単体ではそこまで安くならないものも多くありました。その中で、図面単体でダメなら「2つの部品を1つにしてはどうか」という案が出ました。
下の図をご覧ください。
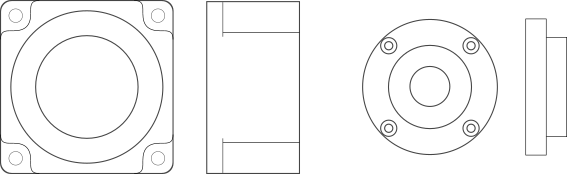
・現状での問題点
2つの部品ははめ合いになっており、「10°のテーパー加工」「半数以上が公差穴」「幾何公差」「外形4隅の掘り込み」と、様々な制度をクリアするために必要な工程が多くなってしまう状況でした。そのため複数の機械・工程を重ねて加工をする必要がありました。
例)部品1:旋盤①、旋盤②、マシニング③ 3工程
部品2:旋盤①、旋盤②、マシニング③、マシニング④ 4工程
納期も余裕があるわけではないし、受注を頂いた段階で間に合うかどうかの調整も必要です。もし間に合わなければ会社としてもせっかくのチャンスを棒に振る形になってしまいます。ですが、例えば「部品2」の場合、1つの工程の為に脱着やデータの用意をする必要があり、「脱着・データ作成」×4人分の時間がかかり、負担は増すばかりです。次第に加工者の時間は減り続け、加工に充てられる時間は少なくなっていき、図面は積み重なり、気持ちが焦ってしまう・・・生産スピードの鈍化だけではなく、ヒューマンエラーの発生原因となる要素が増えてしまいます。このままでは負のスパイラルです。
VE(コストダウン)提案をする際には、お客様の製品の性能を落とさずにコストのみを削減することが大切になってきます。ですがそのために社内の加工者の方に負担をかけていては、いつか回らなくなってしまいます。そこで工程の削減をメインに据え、コストダウンの検討をすることにしました。
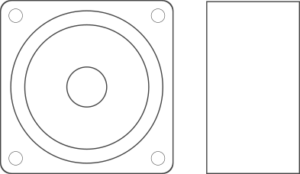
・VE提案内容とその効果
加工の行程を減らすためにまずはめ合いだったものを1部品に設計変更しました(2部品→1部品)。また、統合によって不要になった公差・形状の削減を行いました。結果としては2部品合わせて7工程あったものをたった2工程に集約することができました。
まずは外形4隅の掘り込みに関してですが、これは彫り込まずとも何かに干渉するような部分ではなかったため、A社に確認を取り削除しました。次に公差穴や幾何公差に関しても、1点の部品に統合したため例えば「はめ合い部」にあった「テーパー加工」は不要になり、削除することができました。それぞれ3工程・4工程とかかっていたところを1部品に統合したことで、表と裏の2工程で加工を完結することができました。工程の集約をしたことで、直角度や同軸度などの「幾何公差」は1つの工程で一気に加工することができるため、加工しやすくなり、加工者の負担も削減できました。はめ合いだからこそ必要があった「公差穴」に関しても統合によりその数は半減しました。
また、工程を5つ削減できたことで製作にかかる時間が短縮でき、保守部品の対応で早急に必要になった場合でも無理をせず、迅速な加工から納品につなげることが可能になりました。
・まとめ
結果としては、この部品だけで工程数は7行程→2工程に集約することができました。価格は35%削減。何より工程を集約したことで何度も脱着せず、機械をまたいでの加工がなくなり、幾何公差を出すことが容易にもなりました。コストの削減のみならず加工者の負担を最小限にすることで、コストパフォーマンスの向上を実現することができました。
いかがでしたでしょうか?今回はよくある部品点数の削減提案ではありましたが、公差などの要求精度の高い部分があるからこそ、部品点数削減により加工のしやすさを格段に向上させることができました。これによって加工者への負担は減り、公差が厳しく工程の多い手間のかかる加工→公差は厳しいが加工自体は難しくなく手離れの良い加工へと、部品点数削減によるメリットを最大限に引き出せた提案となりました。もちろんA社も弊社もコストの削減ができたことでWIN-WINです。
コストの削減は大きく、かつ伴う負担は最小限に。この相反するテーマは、コストダウンを考える上で常に付きまといます。皆様も今一度、現状よりベターな方法を探してみてはいかがでしょうか?もし悩むことがございましたら、ぜひこのサイト、「OEM装置 設計・製造.com」をご活用ください!
最後まで読んでいただき、いつもありがとうございます!