投稿日:2022年1月24日
OEM装置設計・製造.comを運営するZESTIA株式会社では材料や購入品の手配に始まり部品加工から電装・組立・調整・据付、そしてお客様への納品までを全て社内一貫対応しています。そのため各加工工程に生じる問題点に対しても設計段階からVA提案を行っています。
今回ご紹介する事例は「設計者様に対する部品共通化提案で、部品コスト25%ダウン、納期10日短縮!」です。ぜひ、生産現場でお役立てください!

設計者によって穴のサイズがバラバラ?
ヒートシール検査装置と呼ばれるシール部を圧着させる機械は、安全性の観点から異物混入や内容物が外部に漏れださないようにシール強度が必要となります。その十分な強度を持たせるためにシール部を圧着する加熱プレートの内部には熱源機構であるヒートシールが挿入されます。
ヒートシール挿入部は細い深穴形状で、深くなればなるほど、ねじれが生じやすくなります。通常ドリルの穴加工では両方向からドリルを貫通させるために狙った位置からズレてしまい要求通りの真直度を出すことが難しく、さらにワイヤー放電加工では真直度は高いですが、加工時間がかなりかかってしまいました。そのためヒートシール挿入部の深穴加工には特殊な工具が必要でした。ただここで問題が発生しており、それが設計担当者によってこの穴サイズがバラバラであったことです。φ8.0~8.4まで寸法範囲が異なり、違うサイズで発注されるたびに工具コストや納期がかかり、大幅なムダがありました。
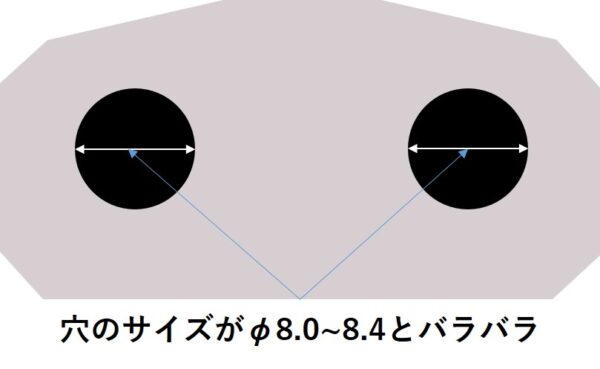
部品コスト25%ダウン、納期10日短縮を実現した提案内容とは?
OEM装置設計・製造.comを運営するZESTIA株式会社では、穴のサイズを設計者同士で共通化出来ていない問題点に対し、設計代表者相談の上で穴のサイズの共通化を目指しました。当社では内部給油装置を保有しており、深穴加工に関する知見があることと同時に、製品製作を全て社内一貫対応することであらゆる角度からの各工程ごとのお客様メリットをご提案しています。そのために設計者の皆様にご安心いただいた上で、部品加工の共通化を実現することが出来ました。
穴のサイズを共通化したことによる導入効果とは?
設計担当者と部品加工の共通化をさせることで生じた導入効果については下記の通りです。いずれにおいても、お客様メリットが非常に高いものです。
①段取り時間を1/2に削減に成功
②完成品納期を10日間短縮に成功
③加工時間を1/3以下に削減成功
④工具の待ち時間0日を実現
※総じて平均25%のコスト削減を実現しました!
まとめ
OEM装置設計・製造.comを運営するZESTIA株式会社では、材料や購入品の手配に始まり部品加工から電装・組立・調整・据付、そしてお客様への納品までを全て社内一貫対応しています。そのため各加工工程に生じる問題点に対しても設計段階からVA提案を行っています。今回の加工形状に対しての最適なアプローチをすることで、お客様のご負担なく大幅なコストメリットが出来る事例とノウハウが多数ございます。製造現場で起きる課題やお困りごとがございましたら、ぜひお気軽にご連絡ください。