投稿日:2023年6月28日
今回は、お客様が外注企業に製作を依頼していた装置の「製造原価」を削減したいとご相談いただき、既存装置の構造見直し(=再設計)をさせていただいた結果、製造原価をおよそ1/2まで削減出来た事例です。
お客様が抱えていた製造原価を高騰させる原因とは?
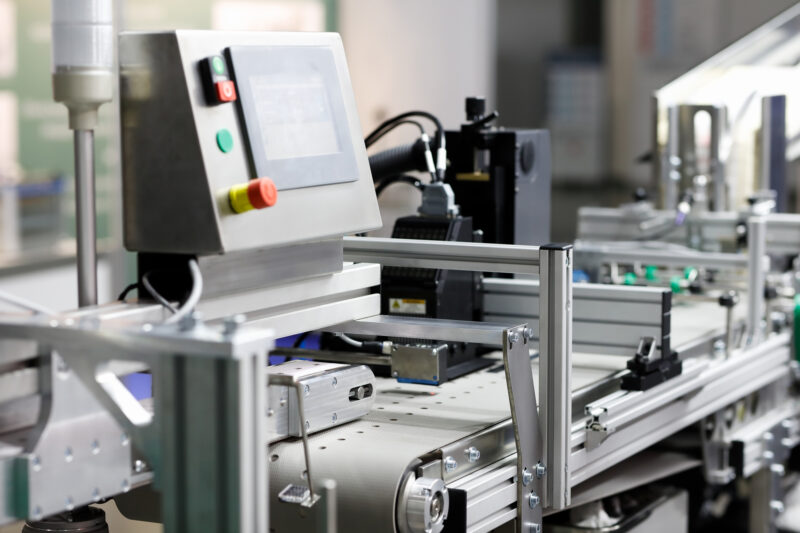
この事例は、半導体装置メーカーである当社のお客様から新機種の装置設計・製造に関する相談をいただいたものです。背景としては、新機種の装置を製造する際に、装置の設計はお客様自身が行いましたが、実際の装置製造は外注先に委託されておりました。しかし、予定されていた1,000万円のターゲットコストを大幅にオーバーしてしまったようで、VE提案を得意とする当社にご相談いただいたという経緯がございました。
そこで、まず当社にて既存装置の構造を確認したところ、以下の理由が製造コストを高騰させている原因だと分かりました。
① 必要以上に装置部品の精度が高い
オーバースペックな設計はよくあります。高機能な装置を製造するとなると、構成される部品の寸法公差や部品形状など、こだわる要素が増えていく傾向があるためです。しかし、実用上必要でない箇所の寸法公差が厳しくなったり、マシンの加工限界を超えてしまうなど、細かな要因の積み重ねでコストはどんどん上がっていきます。
② 装置部品が全てステンレス製である
半導体装置はクリーンルーム等で用いられることを想定し、耐久性・耐食性・防錆が求められ、素材としてはステンレスが使われれることが多いです。しかし、ステンレスの部品加工は材料に粘りがあり、変形しやすい特徴を持つため、加工時間が延びることによるコストアップにつながります。
③ 大きなブロック形状部品に切削指示がある
サイズが大きい部品の切削加工は加工時間がかかる上、材料ロスが大きくコストアップの要因となります。そのため、装置部品のサイズが大きくなるほどに加工コスト・材料費のコストアップとなります。
④ 装置の構造がフレーム構造である
フレーム構造とは装置の「骨組み」のことを指し、多くの装置に採用されています。フレーム構造採用メリットとして、装置部品の重量や振動、また装置と制御装置を繋ぐ電線の重量等、様々な負荷に耐えられる点が装置の信頼性・安全性に直結する特徴があります。しかし堅牢なフレーム構造を形成するための部品製作によって、大きなコストアップ原因を内包した構造とも言えます。
本案件では上記の4点が装置の製造原価を高騰させている要因であると考えられます。高機能な製品を製作するにはそれなりの費用が必要になってきますが、機能を損なわずに適正な原価に収めるのも、設計者の重要な仕事になります。知らず知らずのうちに、非常にコストが高い加工方法で作らざるを得ないような図面を引いてしまっている可能性があるので、「本当に設計上の問題はないか」と吟味することは非常に重要です。
製造原価を1/2にした当社のVE提案とは?
OEM装置設計・製造.comを運営するZESTIA株式会社では、先で洗い出した製造コスト高騰の問題に対して、それぞれ解決提案をいたしました。
① 必要以上に装置部品の精度が高い
⇒ 必要のない公差の削除
一般的に指定公差の数が増えれば増えるほど、加工条件は複雑化します。そこで、重要ではない箇所の公差を除く(もしくは緩和する)ことによって、加工時間の短縮につながります。また公差を満たすための専門工具も必要としない場面も増え、さらなるコストダウンにつながります。
② 装置部品が全てステンレス製である
⇒ オール「ステンレス」から「鉄」や「アルミ」への材質変更
先述の通り、加工難易度・工具消耗度の高い「ステンレス」から優れた切削性と工具消耗度の低い「アルミ」に変更することで加工時間の短縮及び工具の長寿命化につながります。どちらも直接不要コストの削減につながります。
また「ステンレス」から「鉄+表面処理」に変更することで、機能性は維持したまま材料費のコストダウンを実現できます。
③ 大きなブロック形状部品に切削指示がある
⇒ 切削加工から製缶加工への工法転換
比較的サイズの大きな装置部品で、なおかつ直角度や加工面の要求精度が無ければ(又は低ければ)、切削加工から製缶加工に工法転換することで、加工時間と材料費を削減することが可能です。また、形状が複雑な部品は切削加工によって製作を行うと、ロス材が多く加工費も高くなるので、場合によっては部品を個別に分解し、溶接を組み合わせることによって低コストで製作することが可能となります。
④ 装置の構造がフレーム構造である
⇒ 装置構造をモノコック構造に変更
モノコック構造は骨格にあたる部分が一体化している構造になります。モノコック構造を採用することによって、フレームとその他の強度部品を別々に作る必要がないためコストダウンにつながります。強度といえばフレーム構造と考えられがちではありますが、モノコック構造は装置全体が振動しにくい特性を持つので、適宜活用することで最適解を導き出す一助となります。
このように装置を構成する部品を全て見直し、ゼロから装置設計・製造を行った結果、装置の製造コストをおよそ1/2にまで削減させることに成功しました。
装置の設計・製造・組立に関するVE提案
当社が過去にお客様に提案した装置の設計・製造におけるコストダウン事例をご紹介しています。いずれにおいても、お客様メリットが非常に高いものです。
>> 設計変更でコスト1/2・加工時間も1/6を実現した事例!?
>> 図面と製品が別物…‼? 図面の最適化で装置受注率10%UP!!
装置の設計・製造・組立に関するよくある質問
お客様が当社に装置の設計・製造・組立を依頼されるにあたって、よく頂く質問をまとめました。ぜひご確認ください。
まとめ
今回ご紹介したように、当社は装置をただ受託製造しているわけではございません。価格は抑えつつ製品の価値を高めるための工夫が必要となる装置製造において、お客様のご要望に合わせて部品加工から設計を見直すことが出来るのが当社の強みです。製造原価を下げたいというご要望に対して、部品の材質、組立方法、加工方法のいずれかでコスト削減を検討します。中でも機械加工部品を板金部品やロストワックスに置き換えたり、治具で位置出ししている組立部品を治具なしで簡単に組立てられるようにならないかといった視点で各構成要素を見直します。
OEM装置設計 製造.comを運営するZESTIA株式会社は、今回ご紹介する事例のような装置の設計及び既存装置の改造における数多くの事例がございますので、お気軽にご相談ください。