投稿日:2022年10月7日
今回ご紹介するのは、当初コスト面から量産化を見送られたユニットに対して、工程集約により部品点数を削減し、かつ切削加工→切削+板金加工に工法転換することで、結果として機能性を維持した状態でコストを削減できた事例になります。
依頼された真空炉に使用されるアームの1ユニットの一次試作では、要求された性能を満たすことが出来ましたが、量産となると工数が多くコストダウンにあまり貢献出来ませんでした。そのため、装置製造のみならず部品加工から対応することで大幅なコストダウンを実現しました。
その他の装置部品のコストダウン事例については下記をご覧ください。
>> 設計変更でコスト1/2・加工時間も1/6を実現した事例!?
>> 部品コスト25%ダウン、納期10日短縮!?設計者様に対する部品共通化提案
>> 回転部品の10倍長寿命化!?ライフサイクルコスト削減提案
量産化出来ない問題点とは?
ご相談いただいたアルミボックスは中に基板が入る仕様であったために、高いシールド性が求められており、なるべく隙間から電磁波を内外部に通過させないためにも、従来の試作部品メーカーでは6面オール切削にて対応をしておりました。ただ当然のように切削加工では母材から削り出すために、加工時間や材料費等の加工コストが大幅にかかってしまうために、量産する上では不向きな工法でした。一方でコストを削減するために全ての面を板金に置き換えた場合には、組み合わせ時の溶接工程で歪みが発生して組立時に隙間ができることを想定すると、シールド性を満たすためにはそれ相応の時間を要するために適した工法とは言えません。
そこでZESTIAではシールド性を損なわないようにボックスの形状変更を行い、切削加工+板金加工でコストダウンに貢献しました。では、一体どのような形状に変更したことで、コストダウン+シールド性の確保が出来たのか次項でご紹介します。
OEM装置設計・製造.comが提案するコストダウン提案とは?
OEM装置設計・製造.comを運営するZESTIA株式会社では、下図のように側面は曲げ加工+切削加工にて成形し、上下面は切削加工にて成形しました。特に上下面を2層構造に加工することで、側面に対して嵌め込む形で隙間のないシールド性を確保したボックスの製作が可能となりました。このように側面の部品点数を1点削減し、それに伴い工程変更と寸法変更を行うことでコストダウンを実現することに成功しました。
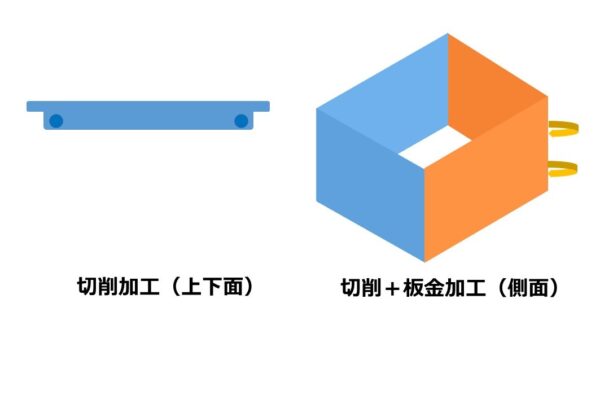
このような部品点数の削減提案はよくあるVA・VE提案ですが、公差などの要求精度の高い部分があるからこそ、部品点数削減により加工のしやすさを格段に向上させることを可能とします。今回ご紹介したように、当社は装置専門で受託製造を行っているわけではございません。価格は抑えつつ製品の価値を高めるための工夫が必要となる装置製造において、お客様のご要望に合わせて部品加工から設計を見直すことが出来るのが当社の強みです。工法転換から材料変更、表面処理までお客様のご要望に多岐にわたる範囲で対応してきた経験から、あらゆる提案が可能ですのでお気軽にご相談ください。